BOTTOM DRIVEN
MINIPILES
Bottom Driven Mini Piles stand out as a cost-effective and eco-friendly alternative among various piling solutions, offering significant advantages over traditional methods.
One of the key benefits of this technique is its efficient use of materials, requiring substantially less concrete or cement compared to other mini piling methods. This not only translates to cost savings but also contributes to environmental sustainability by reducing the overall carbon footprint associated with construction activities.
WHAT THEY’RE USED FOR
Bottom Driven Mini Piles serve as a strategic solution tailored for projects facing challenging ground conditions and spatial constraints. These piles are specifically designed to excel in scenarios where traditional deep foundations are unfeasible or impractical, typically due to restricted access or poor ground conditions.
One of the primary applications of Bottom Driven Mini Piles is within restricted areas, where space limitations pose significant challenges to conventional construction methods. The compact rig size and efficient installation process make them well-suited for deployment in confined spaces such as urban environments, in and around buildings and structures, or areas with limited manoeuvrability and headroom for heavy machinery.
Furthermore, Bottom Driven Mini Piles are particularly effective in addressing poor ground conditions, where unstable or weak soil compositions may be prone to over-flighting where traditional bored piles undermine the ground by taking out too much of the existing ground.
The versatility of Bottom Driven Mini Piles extends to various construction projects, including residential, commercial, and infrastructure developments. Whether used for building foundations, retaining walls, or other structural elements, these piles offer a dependable and cost-effective solution for enhancing the stability and longevity of construction projects.
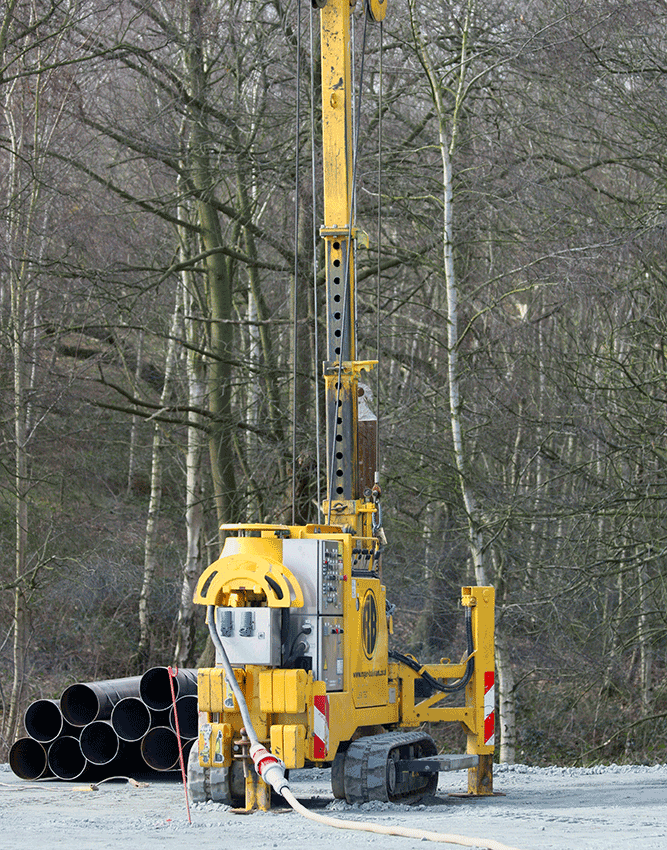
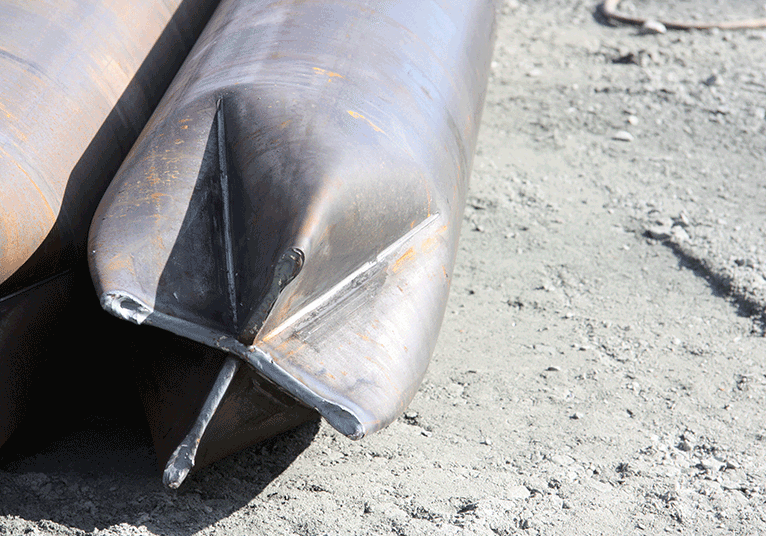
THE PROCESS
The installation process of closed-ended thin-walled steel tube piles involves a series of steps designed to ensure structural integrity and stability. This technique offers numerous advantages over traditional piling methods, making it a preferred choice for projects requiring reliable foundation support.
Initially, a closed-ended thin-walled steel tube is driven into the ground using an internal drop hammer. A dry concrete plug is placed at the bottom of the tube. This serves as a solid base for the internal drop weight to land on and helps prevent soil from entering the tube during installation. The lengths of these tubes typically range between 2 meters and 6 meters, depending on project specifications and soil conditions. As the tube is driven into the ground, it displaces the soil, creating a borehole.
Additional tubes are added using full but non-structural fillet welds as the installation progresses, ensuring a secure and seamless connection between sections, and preventing the ingress of water where present.
As the pile is driven deeper into the ground, additional sections of tube are added as needed until the pile reaches the predetermined set penetration or design length criteria. At this point, the tube is filled with high slump concrete or grout to provide the structural capability and stability.
Finally, a single reinforcement bar or cage is inserted into the filled tube to enhance its structural capacity. This additional reinforcement helps distribute loads throughout the pile, improving its overall performance and longevity.
WHY USE Bottom Driven Minipiles?
- Electrically powered rigs, ideal for indoor construction
- Low CO2 emissions
- Quiet installation
- Minimal site preparation required
- Small lightweight equipment
- Zero spoil
- Environmentally friendly
- Suitable to most ground conditions
EXAMPLE BOTTOM DRIVEN
MINIPILing PROJECTS
ROGER BULLIVANT
QUALITY CONTROL
We successfully deliver projects to the highest standard, safely, on time, within budget, and with care for the environment and communities. Clients choose RB time and time again thanks to our proven track record.
All products are manufactured to BSEN, ISO, and CE accreditation. We are committed to ensuring we continuously deliver high quality, robust service, and product to our clients. At RB we continuously review and access where we can further improve.
We are proud to be recognised and awarded the RoSPA gold award for the sixth year running for the exceptionally high standards towards the health and safety of our employees.